直流无刷电机驱动器的能效提升与节能技术:从原理到应用
在全球碳中和目标的推动下,提升电机系统能效已成为工业、交通和家电领域的核心需求。直流无刷电机(BLDC)凭借其高效率、长寿命和低噪音优势,在各类应用中迅速普及。然而,其驱动器的能效优化仍面临诸多挑战,如功率器件损耗、控制算法滞后、轻载效率低下等问题。本文将深入探讨BLDC驱动器能效提升的关键技术路径、创新方案及产业应用案例。
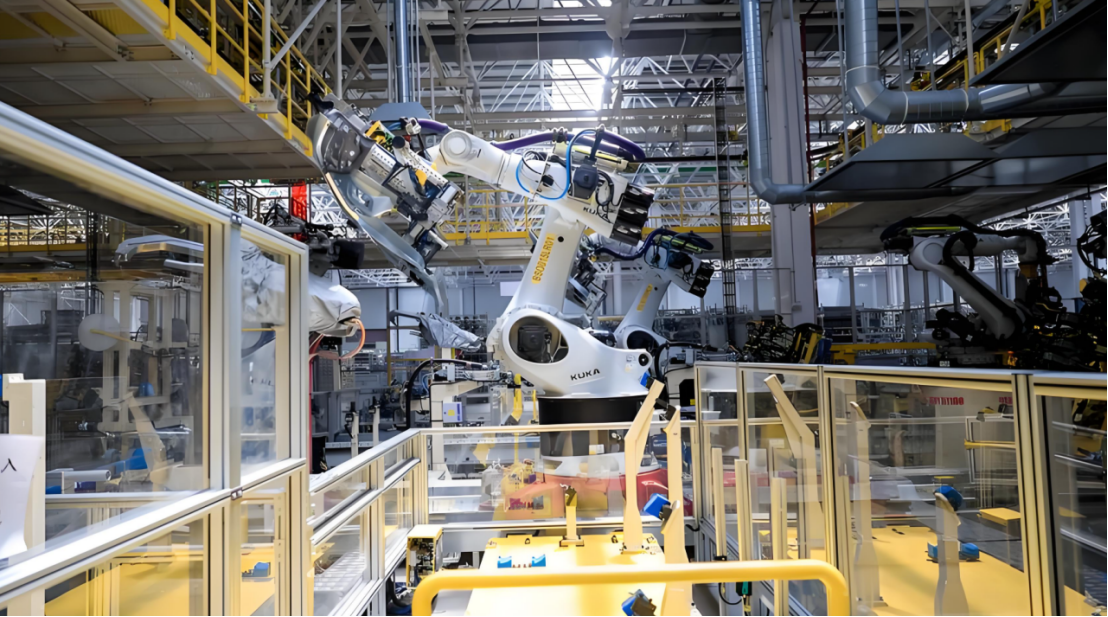
能效损耗机理分析
功率器件损耗功率MOSFET或IGBT的损耗主要包括:导通损耗:与RDS(on)成正比,占总损耗的30%-50% 开关损耗:由寄生电容充放电和二极管反向恢复引起,占40%-60%驱动损耗:栅极电容充放电消耗的能量
控制算法损耗传统六步方波控制存在转矩脉动,导致额外铜损和铁损。而磁场定向控制(FOC)若参数整定不当,会增加d轴电流分量,降低效率。
无源元件损耗滤波电感的铜损和铁损直流母线电容的ESR损耗 PCB走线的电阻损耗
能效提升核心技术宽禁带半导体应用
碳化硅(SiC)MOSFET 优势:开关损耗降低70%,导通电阻比硅MOSFET低50%。案例:意法半导体SCTW12N65G2V2在650V/12A应用中,使驱动器效率从92%提升至96%(@10kHz开关频率)
应用场景:光伏逆变器、电动汽车主驱。氮化镓(GaN)HEMT
优势:超高速开关(<20ns),适合1MHz以上高频应用。案例:EPC2045在3MHz DC-DC转换器中,效率达97.5%,体积比硅方案缩小40%。应用场景:无线充电、LED驱动器
智能控制算法优化
基于模型预测控制(MPC)通过预测电机未来行为优化开关序列,降低电流谐波。实验表明MPC可使电机铁损降低15%-20%(IEEE Trans. on IE, 2023)。自适应效率优化控制根据负载动态调整磁通:轻载时降低磁通减少铁损,重载时增加磁通提升转矩密度。
共直流母线技术多电机系统中,一台电机的制动能量可被其他电机直接利用。 应用:工业自动化生产线、电梯群控系统
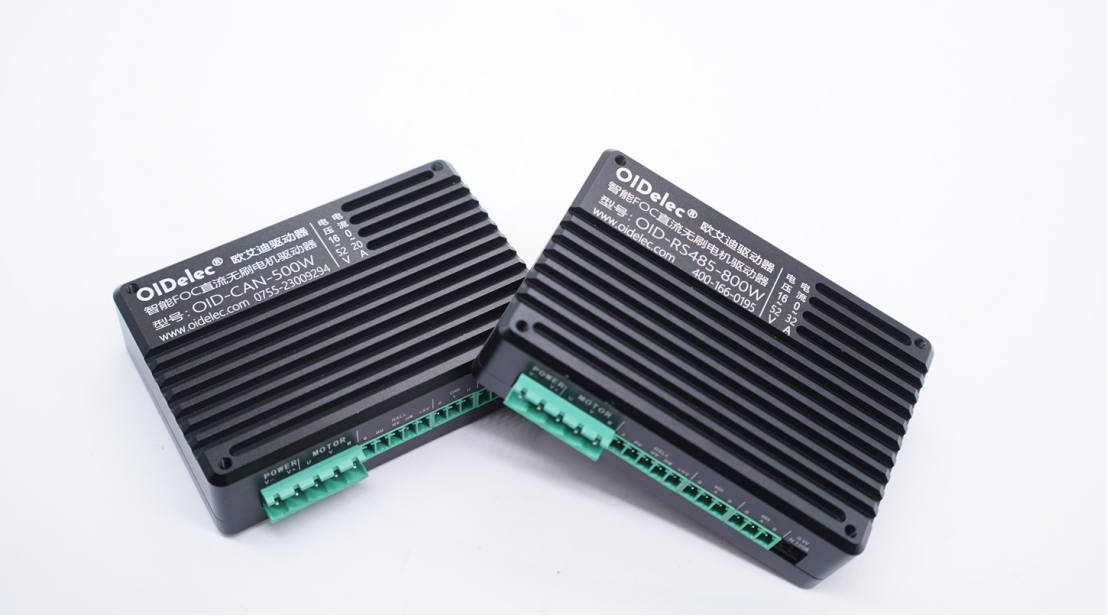
挑战与未来趋势
技术挑战。高频EMI问题:宽禁带器件的高速开关导致更强的电磁干扰。驱动保护设计:SiC/GaN器件对过压过流更敏感,需精密保护电路。成本瓶颈:目前SiC器件价格是硅器件的3-5倍
未来趋势,协同设计 。电机本体与驱动器一体化设计,优化反电动势波形减少谐波损耗
直流无刷电机驱动器的能效提升是一个涵盖材料、器件、电路、算法和系统的多维度工程。宽禁带半导体、智能控制算法和能量回收技术的协同应用,正在推动电机系统能效逼近理论极限。未来,随着技术成熟度提升和成本下降,高能效BLDC驱动系统将在全球能源转型中发挥关键作用,助力实现”双碳”目标。