直流无刷电机驱动器的散热设计
随着工业自动化、新能源汽车、航空航天等领域的快速发展,直流无刷电机因其高效、节能、调速性能好等优点得到了广泛应用。然而,电机驱动器在运行过程中会产生大量热量,如果不能及时有效地散发出去,将会导致驱动器内部温度升高,影响电子元件的性能和寿命,甚至可能引发故障,因此散热设计对于直流无刷电机驱动器至关重要。
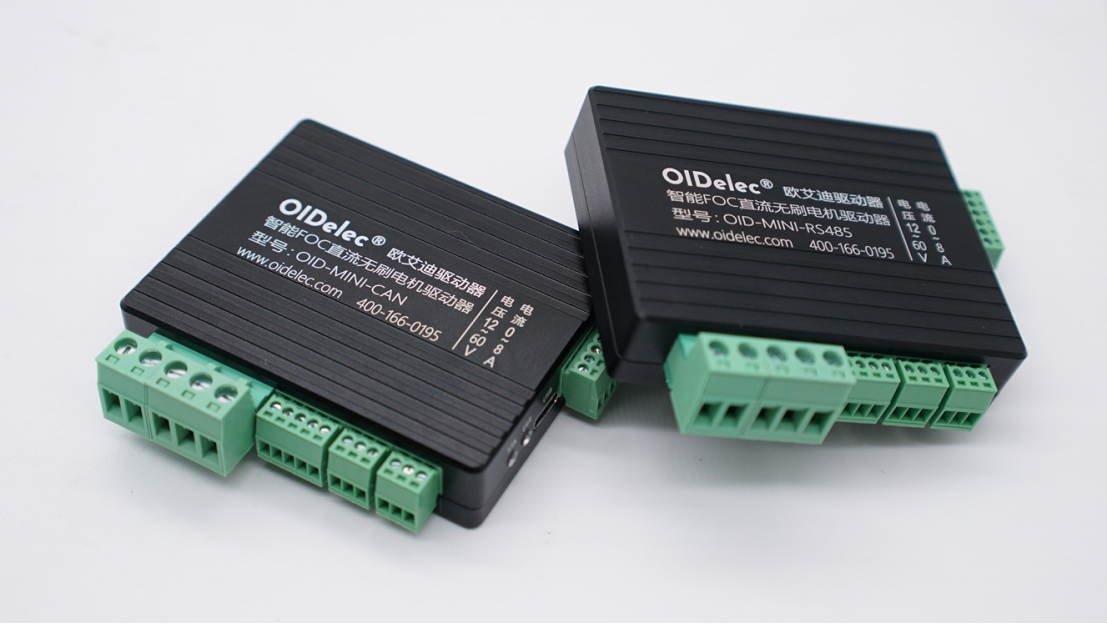
一、直流无刷电机驱动器发热原理及热源分析
(一)发热原理
直流无刷电机驱动器主要由功率开关管、控制电路、电容等电子元件组成。当驱动器工作时,功率开关管不断地导通和截止,将直流电源转换为电机所需的交流电,在这个过程中,由于功率开关管的导通电阻以及开关损耗等,会产生大量的热量,这是驱动器发热的主要原因之一。此外,控制电路中的芯片、电阻等元件在工作时也会消耗一定的功率并产生热量。
(二)主要热源
功率开关管
功率开关管是驱动器中发热最严重的元件之一,其功耗与电机的运行状态、开关频率、电流大小等因素密切相关。在高负载、高转速运行时,功率开关管的发热尤为明显。
续流二极管
续流二极管用于在功率开关管关断时为电机绕组提供续流回路,在续流过程中也会产生一定的功耗和热量,特别是在电机频繁启停或制动时,续流二极管的发热不容忽视。
控制芯片及周边电路
控制芯片负责电机的控制算法实现和信号处理,虽然其单个功耗相对较小,但由于长时间工作以及芯片集成度较高,也会产生一定的热量。同时,周边的电阻、电容等元件的功耗也会对整体发热有所贡献。
二、常见散热方式
(一)自然散热
自然散热是最简单的散热方式,主要依靠驱动器外壳与周围空气的自然对流和热辐射来散发热量。这种散热方式成本低,无需额外的散热装置,但散热效率有限,仅适用于功率较小、发热不太严重的驱动器。例如,一些小型的家用直流无刷电机驱动器,在环境温度较低且负载较小的情况下,可以采用自然散热方式维持正常工作温度。
(二)散热片散热
散热片是一种广泛应用的散热方式,通过增大散热面积,提高热传导效率,将驱动器内部元件产生的热量传导到散热片上,再通过自然对流和热辐射将热量散发到周围环境中。散热片的材料通常为铝合金等导热性能良好的金属,其形状和结构设计会影响散热效果。一般来说,散热片的鳍片数量越多、厚度越薄、间距适当,散热效果越好。例如,在一些工业控制用的直流无刷电机驱动器中,通过在功率开关管等发热元件上安装散热片,能够有效地降低元件温度,提高驱动器的可靠性和稳定性。
(三)风扇散热
风扇散热是利用风扇强制空气流动,加快热量散发的速度。风扇可以将冷空气吹向驱动器,带走热量,使散热效率大大提高。这种散热方式适用于中、大功率的驱动器,或者对温度要求较高的应用场景。风扇的类型有轴流风扇和离心风扇等,轴流风扇风量大、压力低,适用于空间较大且对风阻要求不高的场合;离心风扇压力高、风量相对较小,适合于需要克服一定风阻的紧凑空间。在选择风扇时,需要考虑风扇的风量、风压、噪音、可靠性以及与驱动器的匹配性等因素。例如,在新能源汽车的电机驱动器中,由于功率较大且工作环境较为恶劣,通常会采用风扇散热方式,以确保驱动器在高温环境下能够正常工作。
- 液冷散热
液冷散热是一种高效的散热方式,通过液体(如水、冷却液等)在封闭的管路中循环流动,将驱动器产生的热量带走。液冷散热系统一般包括冷却液、散热器、泵、管道等部件。冷却液在驱动器内部吸收热量后,通过泵的作用输送到散热器中,与外界空气进行热交换,冷却后的冷却液再返回驱动器继续循环散热。液冷散热具有散热能力强、温度均匀性好等优点,适用于大功率、高发热密度的直流无刷电机驱动器,如高性能电动汽车、工业大型设备等领域。然而,液冷散热系统的成本较高、结构复杂,需要专业的设计和维护。
三、散热设计的综合考虑因素
(一)驱动器功率和发热情况
首先要根据直流无刷电机驱动器的额定功率、工作电流、工作电压以及实际运行中的负载情况等因素,准确计算出驱动器的发热量,以此为依据选择合适的散热方式和散热装置的规格参数。例如,对于功率在几百瓦以下的小型驱动器,如果发热不是特别严重,可以优先考虑散热片散热或自然散热;而对于千瓦级以上的大功率驱动器,则可能需要采用风扇散热或液冷散热方式。
(二)工作环境温度和空间限制
工作环境温度对散热效果有很大影响,如果驱动器工作在高温环境中(如工业炉窑附近、高温车间等),则需要更强的散热能力来保证其正常工作温度。同时,还要考虑驱动器的安装空间限制,选择合适尺寸和形状的散热装置,确保其能够在有限的空间内安装并正常工作。例如,在一些航空航天设备中,由于空间有限且对重量有严格要求,散热设计需要在保证散热效果的前提下,尽可能减小散热装置的体积和重量,可能会采用高导热率的材料和紧凑的散热结构设计。
(三)成本和可靠性
散热设计需要在成本和可靠性之间进行平衡。不同的散热方式成本差异较大,如自然散热成本最低,液冷散热成本最高。在满足驱动器散热要求的前提下,应选择成本合理的散热方案,同时要考虑散热装置的可靠性和寿命,避免因散热装置故障而导致驱动器损坏。例如,在一些对成本敏感的民用产品中,如小型电动工具的电机驱动器,会优先选择性价比高的散热片散热方式,并通过优化散热片的设计来提高散热效果。
(四)电磁兼容性(EMC)
在散热设计过程中,还需要考虑散热装置对驱动器电磁兼容性的影响。例如,金属散热片可能会对驱动器内部的电磁场分布产生一定的影响,从而影响驱动器的正常工作或产生电磁干扰。因此,在设计散热片的形状、尺寸和安装位置时,需要进行电磁兼容性分析和优化,采取必要的屏蔽措施,如在散热片表面涂覆电磁屏蔽涂层或增加屏蔽罩等,以确保驱动器的电磁兼容性符合相关标准要求。

四、散热设计案例分析
以一款用于工业机器人关节驱动的直流无刷电机驱动器为例,该驱动器额定功率为 1.5kW,工作电流为 10A,工作环境温度范围为 -10℃至 40℃,安装空间有限且对可靠性要求较高。
(一)散热方式选择
考虑到驱动器的功率和工作环境,选择了风扇散热方式。选用了一款尺寸合适、风量为 50CFM(立方英尺每分钟)、风压为 100Pa 的轴流风扇,风扇安装在驱动器外壳的一侧,通过风道设计使冷空气能够均匀地流过功率开关管、续流二极管等主要发热元件,然后从另一侧排出。
(二)散热片设计
在功率开关管和续流二极管等发热严重的元件上安装了铝合金散热片,散热片采用了鳍片式结构,鳍片厚度为 1mm,间距为 3mm,高度为 30mm,总散热面积达到了 200cm²。通过优化散热片与元件之间的接触热阻,采用导热硅脂填充间隙,提高了热传导效率。
(三)温度监测与控制
为了确保驱动器的温度在安全范围内,在驱动器内部安装了温度传感器,实时监测关键部位的温度。当温度超过设定的阈值(如 80℃)时,通过控制电路降低电机的输出功率,同时提高风扇的转速,加强散热效果;当温度降低到安全范围内后,再恢复电机的正常运行功率。
通过以上散热设计方案的实施,该直流无刷电机驱动器在额定工况下的最高温度从原来的 100℃以上降低到了 70℃左右,有效提高了驱动器的可靠性和稳定性,满足了工业机器人关节驱动的要求。
五、结论
直流无刷电机驱动器的散热设计是保证其高效稳定运行的关键环节。通过对发热原理和热源的深入分析,结合实际应用中的各种因素,选择合适的散热方式,并进行合理的散热结构设计和优化,可以有效地降低驱动器内部温度,提高电子元件的寿命和可靠性,从而提升整个直流无刷电机系统的性能。在未来的发展中,随着直流无刷电机在更多领域的广泛应用以及对功率密度和可靠性要求的不断提高,散热设计将面临更多的挑战和机遇,需要不断地进行技术创新和优化,以满足不同应用场景的需求。